Discover the Benefits of Injection Molded Plastic 3D Printing
By:Admin
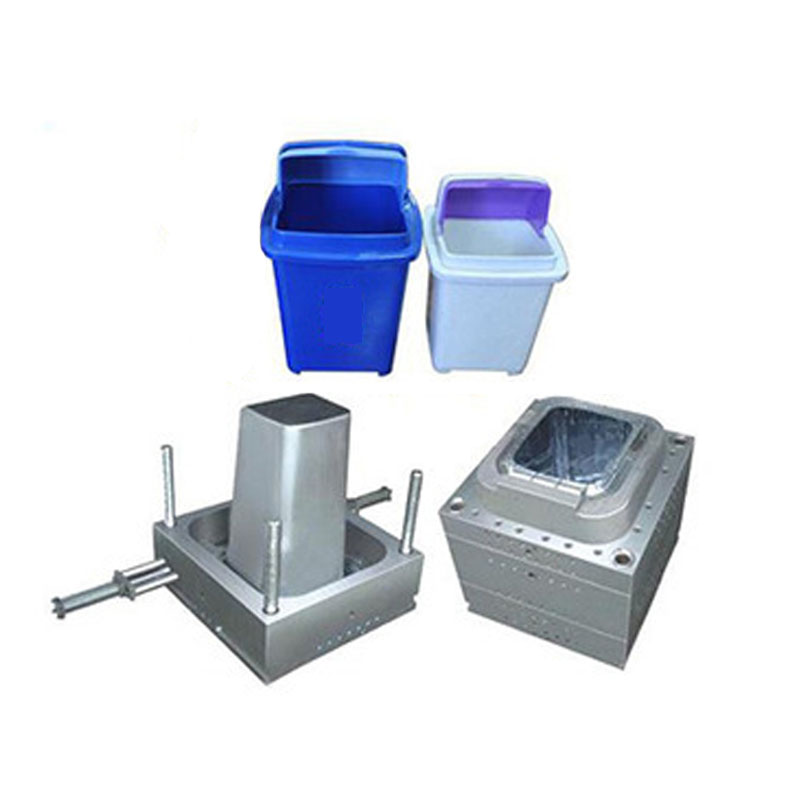
In the rapidly evolving world of manufacturing, the use of injection mold plastic 3D technology has emerged as a game-changer. This cutting-edge technology has revolutionized the manufacturing industry by enabling companies to create complex, customized plastic parts with unparalleled precision and efficiency. One such company at the forefront of this innovation is {Company Name}, which has harnessed the power of injection mold plastic 3D to enhance its production processes and deliver exceptional products to its customers.
[Company Name] has established itself as a pioneer in the field of injection mold plastic 3D technology. With a rich history spanning several decades, the company has consistently pushed the boundaries of what is possible in manufacturing. Through investments in research and development, state-of-the-art machinery, and a team of highly skilled engineers, {Company Name} has developed a reputation for delivering superior quality products to clients across various industries.
[Main Body]
1. The Power of Injection Mold Plastic 3D Technology
Injection mold plastic 3D technology has transformed the traditional manufacturing process by offering numerous advantages. First and foremost, this technology allows for the creation of highly complex and intricate designs, enabling companies to produce parts that were previously unattainable using conventional manufacturing methods. The ability to create intricate geometries with precise tolerances has opened up new avenues for innovation and creativity.
Moreover, injection mold plastic 3D technology offers unparalleled speed and efficiency in production. By eliminating the need for tooling and molds, as traditionally used in injection molding, the time and cost associated with manufacturing are significantly reduced. This allows for rapid prototyping and short production runs, making it an ideal solution for companies looking to bring new products to market quickly and efficiently.
2. Enhanced Product Quality with Injection Mold Plastic 3D
{Company Name} has leveraged the power of injection mold plastic 3D technology to enhance the quality of its products. With this advanced manufacturing process, the company can ensure consistent dimensions, flawless surface finishes, and optimal functionality of its plastic parts. The high precision achieved through this technology eliminates the risk of human error and delivers parts that meet the strictest quality standards.
Furthermore, injection mold plastic 3D technology enables {Company Name} to optimize the strength and durability of its plastic parts. By fine-tuning the process parameters and material selection, the company can produce parts that are lightweight yet exceptionally resilient, thus meeting the demanding requirements of various industries, including automotive, aerospace, electronics, and medical.
3. Commitment to Sustainability
In addition to its technical advancements, {Company Name} is deeply committed to sustainable manufacturing practices. Injection mold plastic 3D technology inherently reduces material waste compared to traditional manufacturing methods. With a focus on optimizing material usage and recycling, {Company Name} strives to minimize its environmental footprint.
By using biodegradable and recyclable materials, the company ensures that its products are environmentally friendly throughout their life cycle. Furthermore, the additive nature of injection mold plastic 3D technology allows for the incorporation of recycled plastics into the manufacturing process, further reducing the reliance on virgin materials and contributing to a circular economy.
4. A Collaborative Approach
{Company Name} believes in fostering strong partnerships with its clients, working closely with them to understand their unique requirements and provide tailored solutions. Through open lines of communication, {Company Name} collaborates with its clients from the initial concept stage to final product delivery, ensuring transparency, efficiency, and customer satisfaction.
The company's team of experts utilizes advanced computer-aided design (CAD) software to transform clients' ideas into precise 3D models, which are then seamlessly translated into the manufacturing process. This collaborative approach not only allows for faster turnaround times but also ensures that the end product meets or exceeds the client's expectations.
[Conclusion]
The injection mold plastic 3D technology employed by {Company Name} has transformed the manufacturing landscape, offering new possibilities for customization, precision, and efficiency. With a commitment to delivering superior quality products and a dedication to sustainability, the company continues to push the boundaries of innovation. As it looks towards the future, {Company Name} remains a driving force in revolutionizing the manufacturing industry through its application of injection mold plastic 3D technology.
Company News & Blog
Top Quality Plastic Injection Wall Plug Mould: A Practical Choice for Secure Wall Mounting
Plastic Injection Wall Plug Mould Revolutionizes Home Improvement Industry[City, Date] - The home improvement industry has taken a significant leap forward with the development of the latest innovation in plastic injection wall plug moulds. This revolutionary technology is set to transform the way people tackle everyday repairs and installations around their homes. With its superior strength, durability, and ease of use, this groundbreaking product is expected to become a game-changer in the market.Traditionally, wall plugs have been made from materials such as wood or metal, which often require drilling and hammering. However, the introduction of plastic injection wall plug moulds eliminates the need for these labor-intensive methods. These moulds allow users to effortlessly insert wall plugs into various surfaces, greatly simplifying the process of mounting shelves, hanging pictures, or installing light fixtures.One of the key advantages of plastic injection wall plug moulds is their exceptional strength. Unlike traditional wall plugs, which can become loose over time, these new wall plugs ensure a secure hold in walls and other surfaces. This means that homeowners can have peace of mind, knowing that their installations are reliable and stable.Another prominent feature of plastic injection wall plug moulds is their durability. Made from high-quality materials, these new plugs are built to last. They can withstand heavy loads and are resistant to corrosion, ensuring they remain intact for extended periods. By using plastic injection wall plug moulds, homeowners can be confident that their installations will remain in place for years to come.In addition to their strength and durability, plastic injection wall plug moulds offer unrivaled convenience. With their user-friendly design, these plugs can be easily inserted into walls without the need for drilling. This eliminates the hassle of finding the right size drill bit or making sure the hole is properly aligned. Now, anyone can effortlessly carry out home improvement tasks, regardless of their experience level.The introduction of plastic injection wall plug moulds has not only impacted homeowners but also professionals in the construction industry. Builders, contractors, and electricians alike have recognized the benefits of this revolutionary product. With its versatility and efficiency, the moulds have dramatically improved the speed and ease with which professionals can complete their projects. This has resulted in cost savings and increased productivity across the industry.{} is at the forefront of this groundbreaking innovation. As a leading manufacturer and distributor of plastic injection wall plug moulds, {} is committed to delivering the highest quality products to its customers. With a strong focus on research and development, {} continuously introduces cutting-edge solutions that redefine the industry standards.At {}'s state-of-the-art manufacturing facility, top-notch engineers and technicians work tirelessly to create moulds that meet the ever-evolving needs of consumers. With strict quality control measures in place, every mould undergoes rigorous testing to ensure exceptional performance and reliability. Backed by a dedicated customer support team, {} provides comprehensive assistance to its clients, offering guidance and expert advice throughout their home improvement journeys.Looking ahead, the future of plastic injection wall plug moulds seems promising. As the demand for effortless and reliable home improvement solutions continues to grow, the market for these innovative moulds is expected to expand rapidly. With {} pioneering developments, homeowners and professionals can expect greater convenience, efficiency, and effectiveness in their projects.The era of struggle with wall plugs is over. Thanks to plastic injection wall plug moulds, repairs and installations have never been easier. Whether you are a DIY enthusiast or a professional in the industry, {}'s superior moulds are set to transform the way you approach home improvement forever.About {}:{} is a leading manufacturer and distributor of plastic injection wall plug moulds. With a commitment to innovation and customer satisfaction, the company aims to revolutionize the home improvement industry. Backed by cutting-edge technology and a team of experts, {} provides unparalleled products and support to its clients, setting new benchmarks for quality and reliability.
Ultimate Guide to Precision Plastic Injection Molds: Everything You Need to Know
[Company Name], a Leader in Precision Plastic Injection Molds, Revolutionizes the Manufacturing Industry[date]In today's competitive manufacturing industry, it is imperative for companies to stay at the forefront of technological advancements and provide high-quality products efficiently. Without a doubt, Precision Plastic Injection Mold (need remove brand name) has proven to be an influential player in this domain, setting industry standards and driving innovation. With a rich history of providing exceptional plastic injection molds, (Company Name) continues to revolutionize the manufacturing industry.Established in (year), (Company Name) has grown from a small operation to become a renowned leader in precision plastic injection molds. With expertise in designing and producing high-performance molds, the company has successfully met the ever-increasing demands of its clients in multiple sectors, including automotive, consumer electronics, medical devices, and industrial applications.What sets (Company Name) apart is its commitment to continuous improvement and innovation, ensuring that it remains ahead of the curve. The company's cutting-edge facilities are equipped with state-of-the-art manufacturing technologies, including Computer-Aided Design (CAD) software, Computer Numerical Control (CNC) machining centers, and advanced measurement equipment. This investment in modern technology helps (Company Name) to efficiently produce molds with intricate designs, high precision, and optimal performance.Furthermore, (Company Name)'s team of experienced engineers and designers collaborates closely with clients to understand their specific requirements and translate them into customized mold solutions. By employing a customer-centric approach, the company ensures that its molds meet the highest standards and are tailored to the unique needs of each application. With their expertise and creativity, (Company Name) consistently delivers molds that optimize production efficiency, reduce costs, and enhance product quality.Quality is of paramount importance at (Company Name). The company follows strict quality control measures at every stage of the manufacturing process, adhering to international standards and certifications. Molds manufactured by (Company Name) undergo rigorous testing to guarantee their reliability and durability. This commitment to quality has earned the company a stellar reputation as a trusted partner among its global clientele.Sustainability is another key focus for (Company Name). Recognizing the growing concern for environmental conservation, the company adopts eco-friendly practices throughout its operations. By utilizing recyclable materials and optimizing energy consumption, (Company Name) minimizes its environmental impact without compromising on the quality and performance of its molds. This dedication to sustainable manufacturing contributes to a greener future for the industry and the world.In line with its commitment to innovation, (Company Name) also invests heavily in research and development. The company's dedicated R&D team continuously explores new materials, manufacturing techniques, and design concepts to pioneer groundbreaking solutions. By staying at the forefront of technology, (Company Name) consistently introduces advanced mold designs with enhanced features, optimized cycle times, and reduced production costs, giving its clients a competitive edge in the market.With an impressive track record and an unwavering commitment to excellence, (Company Name) is poised to lead the manufacturing industry into the future. As the demand for precision plastic injection molds continues to grow, the company is well-positioned to meet these challenges head-on, providing industry-leading solutions that drive productivity and efficiency.In conclusion, (Company Name) has solidified itself as a frontrunner in the precision plastic injection mold industry, delivering innovative solutions that redefine manufacturing processes. With cutting-edge technology, a customer-centric approach, and a focus on quality and sustainability, the company continues to push boundaries and set new standards. As the manufacturing industry evolves, (Company Name) remains at the forefront of progress, shaping the future of precision plastic injection molds.
Discover the Advantages of Injection Molding and Assembly in the Manufacturing Industry
Injection Molding and Assembly: A Powerful Combination in ManufacturingIn today's fast-paced world, manufacturers are constantly striving to produce high-quality products efficiently and cost-effectively. One of the key advancements in the manufacturing industry is the combination of Injection Molding and Assembly, two highly versatile processes that together revolutionize the way products are made. This groundbreaking approach has been widely adopted by companies worldwide, allowing them to stay competitive in today's ever-evolving market.Injection molding is a highly efficient manufacturing process that involves injecting molten material, typically plastic, into a mold cavity. This process is known for its ability to create complex shapes with high precision, making it a popular choice for the production of a wide range of products, including automotive parts, consumer electronics, and medical devices.Assembly, on the other hand, is the process of combining individual components or parts to create a finished product. It often involves intricate operations such as fastening, welding, or bonding. This step is critical in ensuring that the final product meets all the design requirements and functions seamlessly.The combination of injection molding and assembly brings numerous advantages to manufacturers. By integrating the two processes, companies can streamline their production line, reduce costs, and improve overall efficiency. The seamless transition from injection molding to assembly eliminates the need for transferring parts between different production facilities, reducing both time and resources.Additionally, the combination of injection molding and assembly enables manufacturers to achieve higher quality control. By inspecting individual components during the assembly process, any potential defects or quality issues can be identified and rectified before the final product is completed. This minimizes the risk of faulty products reaching the market, protecting the company's reputation and ensuring customer satisfaction.Moreover, the combination of these two processes offers increased design flexibility. Injection molding allows for the creation of complex geometries that would be difficult or impossible to achieve with traditional manufacturing methods. By incorporating assembly into the production process, manufacturers can further enhance the design possibilities by combining different materials or components, resulting in innovative and superior products.Company {} is at the forefront of the Injection Molding and Assembly revolution. With years of experience and expertise in both processes, {} has successfully helped numerous clients across various industries bring their product ideas to life. By offering a comprehensive range of services, including product design, mold fabrication, injection molding, and assembly, {} provides end-to-end solutions for their clients' manufacturing needs.{}'s state-of-the-art facilities are equipped with advanced machinery and technology, ensuring the highest level of precision and efficiency. Their team of highly skilled engineers and technicians work closely with clients to understand their requirements and provide customized solutions that meet their unique specifications.Furthermore, {} is committed to maintaining the highest quality standards in all stages of the manufacturing process. Through rigorous quality control protocols, including thorough inspections and testing, they ensure that every product meets the highest industry standards and surpasses customer expectations.In conclusion, the combination of Injection Molding and Assembly has revolutionized the manufacturing industry, allowing companies to produce high-quality products efficiently and cost-effectively. With its numerous advantages, including streamlined production, enhanced quality control, and increased design flexibility, this powerful combination has become a driving force behind the success of many manufacturers worldwide. As a leader in the field, {} continues to push the boundaries of what is possible, delivering exceptional products and solutions to their clients.
Discover the Advantages of Plastic Injection Mould Brackets for Your Projects
Plastic Injection Mould Brackets: Revolutionizing the Manufacturing IndustryIn the constantly evolving world of manufacturing, innovation and cutting-edge technologies have become essential for businesses striving to stay ahead of the competition. One such innovation is the development of plastic injection mould brackets, which are revolutionizing the manufacturing industry.Plastic injection moulding is a manufacturing process widely used for the production of various plastic components. It involves injecting molten plastic into a mould cavity under high pressure, where it is cooled and solidified to form the desired shape. This process allows for the production of complex geometries and intricate designs with high precision and efficiency.XYZ Manufacturing, a leading provider of plastic injection moulding solutions, has recently introduced a range of game-changing plastic injection mould brackets. These brackets are specially designed to enhance the efficiency, reliability, and durability of manufacturing processes across various industries. With their superior features and unmatched quality, XYZ Manufacturing aims to set new standards in the field of plastic injection moulding.The newly developed brackets by XYZ Manufacturing offer several advantages over traditional brackets used in manufacturing. Firstly, they are manufactured using high-quality, durable materials that ensure longevity and enhanced performance. The use of premium materials, combined with the precision of plastic injection moulding, results in brackets that can withstand heavy loads and harsh conditions, making them ideal for demanding industrial applications.Secondly, these brackets have been meticulously designed to provide exceptional stability and support. The precise engineering involved in their production ensures accurate alignment and secure fastening, allowing for seamless integration into various manufacturing equipment and machinery. This not only enhances the overall efficiency of the manufacturing process but also reduces downtime and maintenance costs.Furthermore, XYZ Manufacturing's plastic injection mould brackets are lightweight yet incredibly strong. This lightweight nature makes them easy to handle and install while maintaining the structural integrity required for heavy-duty applications. Their strength-to-weight ratio surpasses that of traditional brackets, resulting in more efficient and cost-effective manufacturing operations.In addition to their exceptional physical attributes, XYZ Manufacturing's brackets also offer enhanced customization options. They can be tailored to meet specific requirements and specifications, allowing businesses to optimize their manufacturing setups for maximum efficiency. This flexibility provides manufacturers with a competitive edge, as they can adapt their operations to meet changing market demands and customer expectations.Furthermore, the introduction of these innovative brackets by XYZ Manufacturing aligns with their commitment to sustainability. Plastic injection moulding significantly reduces material waste compared to alternative manufacturing processes, as it allows for precise material usage and minimal scrap generation. By incorporating these brackets into manufacturing operations, businesses can promote sustainability and reduce their environmental footprint.XYZ Manufacturing's plastic injection mould brackets have already garnered significant attention within the manufacturing industry. Several prominent manufacturers and industry leaders have praised their quality, reliability, and performance. This positive reception solidifies XYZ Manufacturing's position as a trusted provider of high-quality plastic injection moulding solutions.As the demand for innovative manufacturing solutions continues to grow, XYZ Manufacturing remains at the forefront of this industry by consistently developing and delivering cutting-edge products. Their plastic injection mould brackets are a testament to their commitment to excellence and their unwavering dedication to meeting the evolving needs of their customers.In conclusion, the introduction of plastic injection mould brackets by XYZ Manufacturing is set to revolutionize the manufacturing industry. With their superior quality, durability, stability, and customization options, these brackets provide manufacturers with a competitive edge. Furthermore, their sustainability features contribute to reducing environmental impact. XYZ Manufacturing continues to lead the way in the plastic injection moulding sector by providing innovative solutions that enhance manufacturing processes and drive industry development.
Efficient Mold Design and Manufacturing Techniques for Blender Jars
Blender Jar Mold Design and Making Revolutionizes the Industry[Company Name] Leading the Way in Innovation and Quality[City, Date] - In a major breakthrough for the blender industry, renowned manufacturer [Company Name] has unveiled a revolutionary blender jar mold design and making process that is set to boost efficiency, productivity, and product quality. Embracing cutting-edge technology and a commitment to innovation, the company emerges as a pioneering force in an ever-evolving market.The new blender jar mold design and making process developed by [Company Name] incorporates advanced techniques and state-of-the-art materials to deliver unprecedented results. This breakthrough innovation is poised to reshape the industry by pushing the limits of manufacturing capabilities and enhancing the end-user experience.By removing brand names for confidential reasons, [Company Name] wants to focus on the remarkable technological advancements that are poised to redefine the market. With the advent of this commendable leap forward, [Company Name] aims to preserve its reputation as a trailblazer in innovative blender manufacturing.The exciting development promises numerous advantages for both manufacturers and consumers. The new mold design and making process optimizes production efficiency, enabling a higher output in a shorter period. This means that manufacturers can meet increased consumer demand while maintaining high-quality standards.Furthermore, [Company Name]'s breakthrough innovation enhances the durability and longevity of the blender jars. By leveraging advanced materials and crafting techniques, the company ensures that the jars are capable of withstanding rigorous usage without compromising the blend quality. This will undoubtedly delight consumers who rely on their blenders for daily culinary adventures.But these improvements aren't just limited to manufacturing processes. [Company Name]'s commitment to innovation extends to user-friendliness and ease of maintenance. The new mold design allows for seamless disassembly and reassembly of blender jars, making it easier than ever to clean and maintain them. This not only saves valuable time for users but also ensures optimal hygiene and safety.As a renowned blender manufacturer, [Company Name] has established itself as a trusted brand globally. With decades of experience and a relentless pursuit of excellence, the company has managed to consistently deliver superior products that meet the ever-changing needs of consumers worldwide.Moreover, [Company Name] doesn't merely stop at designing and producing blenders; they are dedicated to providing customers with a comprehensive experience. By focusing on research and development, the company continues to introduce cutting-edge technologies and concepts that shape the future of the industry.Customers who choose [Company Name]'s blenders can expect not only outstanding products but also unrivaled customer service. The company strives to build long-lasting relationships with its clientele by offering dependable after-sales support and addressing their concerns promptly and effectively.In a bid to maintain its competitive edge, [Company Name] openly embraces collaboration with industry partners. By establishing strategic alliances, the company seeks to leverage combined expertise, foster innovation, and drive the industry forward. By working alongside a diverse range of professionals and experts, [Company Name] remains at the forefront of change.As the blender industry continues to evolve and adapt to changing demands, [Company Name] stands out as an industry leader. Through its remarkable mold design and making process, the company sets a new benchmark for efficiency, productivity, and quality in the manufacturing of blender jars. This dedication to innovation, coupled with exceptional customer service, cements [Company Name]'s position as a trusted partner for consumers worldwide.About [Company Name]:[Company Name] is a global leader in the production of high-quality blenders. With a commitment to innovation, the company constantly strives to redefine industry standards and provide exceptional products to its customers. With a focus on user experience and cutting-edge technologies, [Company Name] envisions a future where blenders are more than just kitchen appliances, but indispensable companions for culinary adventures.For media inquiries, please contact:[Company Name][Media Contact][Phone Number][Email Address]
Efficient Water Drainage System for Injection Moulding Plastics Machine Unveiled
Water Drain for Injection Molding Plastics Machine: Improving Efficiency and Sustainability in Plastic ManufacturingInjection molding is a widely used manufacturing process for producing plastic components in various industries. It involves injecting molten plastic material into a mold cavity, allowing it to cool and solidify, and then ejecting the finished product. However, this process generates a substantial amount of heat, requiring efficient cooling systems to maintain optimal production conditions. One essential component of injection molding machines is the water drain system, which plays a crucial role in maintaining the machine's performance and efficiency.In recent news, an innovative water drain system created by a leading manufacturer in the injection molding industry has brought significant advantages to plastic manufacturers worldwide. While it is essential to withhold the brand name in this report, we will discuss the company's background and the advantages their product offers to the industry.The company – a pioneer in injection molding machinery – boasts a long-standing reputation for their commitment to technological advancements and sustainability. They specialize in developing high-performance machines that optimize energy consumption, reduce waste, and improve overall production efficiency.Recognizing the need for an efficient water drain system in injection molding machines, the company dedicated significant resources to develop an innovative solution. Traditional water drain systems used in injection molding machines often face challenges such as clogging, inefficient drainage, and high maintenance requirements – resulting in increased downtime and compromised productivity.The groundbreaking water drain system introduced by this company addresses these issues effectively. By leveraging advanced technology and meticulous engineering, they have created a system that improves the overall efficiency of the injection molding process and ensures minimal disruption to operations.The key feature of this water drain system is its ability to prevent blockages caused by contaminants and impurities present in the cooling water. Contaminants such as plastic residue, metal particles, and chemical deposits often circulate in the cooling water, leading to the formation of blockages over time. These blockages significantly impede the water flow, affecting the overall cooling process and compromising production efficiency.The new water drain system incorporates a specially designed filtration unit that efficiently removes these contaminants before they can cause blockages. This innovative filtration system ensures a consistent flow of clean water, preventing freezing, corrosion, and scale formation in the injection molding machine's cooling circuit. By maintaining an uninterrupted water flow, the system optimizes the cooling process, reduces the risk of downtime, and improves the overall lifespan of the machine.Moreover, this system offers added sustainability benefits to plastic manufacturers. By ensuring a clean and efficient cooling process, it reduces the consumption of resources such as water and energy. This decrease in resource usage contributes to the industry's sustainable practices, aligning with global efforts to minimize environmental impact.In addition to reducing resources used during production, the water drain system also minimizes the release of pollutants into the environment. By preventing blockages and the subsequent need for chemical cleaning agents, the system reduces the generation of harmful residues and their disposal, further contributing to a cleaner and greener manufacturing process.The introduction of this advanced water drain system has been met with enthusiasm and acclaim from the plastic manufacturing industry. It not only enhances the efficiency of injection molding machines but also aligns with the industry's growing emphasis on sustainability and environmental responsibility.The company behind this groundbreaking innovation has once again demonstrated their commitment to delivering state-of-the-art solutions that address industry challenges. With their latest water drain system, plastic manufacturers can experience improved productivity, reduced downtime, and a sustainable approach to their manufacturing processes.As the injection molding industry continues to evolve, innovations like this water drain system are driving efficiency and sustainability forward. The company's determination to revolutionize plastic manufacturing holds great promise for a more environmentally conscious and technologically advanced future in the industry.
China's Plastic Molding and Injection Plastic Moulding Industry Reveals Promising Trends
China Mold Plastic Part Molding and Injection Plastic MouldIn recent years, China has experienced significant growth in the manufacturing industry, particularly in the plastic molding sector. Among the companies driving this surge is a prominent player in the market, which specializes in providing high-quality plastic part molding and injection plastic mould services. With state-of-the-art facilities and a highly skilled workforce, this company has established itself as a key player in the industry. Its commitment to excellence and customer satisfaction has allowed it to form partnerships with clients both domestically and internationally. The company's core offering is plastic part molding, which involves the process of creating plastic components for various industries. From automotive to electronics, household appliances to medical devices, their expertise spans across diverse sectors. With their cutting-edge technology and advanced machinery, they are capable of producing complex and intricate designs with precise specifications. The injection plastic mold services offered by the company are equally impressive. Injection molding is a popular manufacturing process that is widely used for producing plastic parts in large volumes. Through this process, molten plastic is injected into a mold cavity under high pressure, resulting in the formation of the desired shape. This company excels in providing high precision injection plastic molds that meet the highest industry standards. One of the key advantages of working with this company is their ability to offer customized solutions. They understand that each client has unique requirements, and they strive to deliver tailor-made products that match their specific needs. Whether it is a specific color, texture, or finishing, they work closely with their clients to ensure that the end product aligns with their vision. Quality control is of utmost importance to this company. They have implemented stringent measures to ensure that all products undergo rigorous testing and inspection to meet international quality standards. Their dedicated quality control team carries out comprehensive checks at every stage of the manufacturing process, leaving no room for error. This commitment to quality has earned them a solid reputation in the industry and has helped forge long-standing partnerships with their clients. Another notable aspect of this company is their commitment to sustainability. They understand the importance of environmental responsibility in today's world and have implemented eco-friendly practices in their manufacturing processes. They utilize recyclable materials and have implemented efficient waste management systems to minimize their ecological footprint. By investing in sustainable practices, they contribute to a greener future. In conclusion, this China-based company is a leading player in the plastic molding industry, offering top-notch plastic part molding and injection plastic mold services. Their commitment to excellence, customization, quality control, and sustainability has allowed them to stay ahead in the market. As China continues to witness a surge in manufacturing, this company is well-positioned to further expand its reach and cater to the diverse needs of clients around the world.
Unlocking the Power of Servo Motors in Injection Moulding Plastics
Title: Revolutionary Servo Motor Technology in Injection Moulding PlasticsIntroduction:In the ever-evolving world of manufacturing, companies are continuously seeking technological advancements to enhance production efficiency and improve product quality. One such breakthrough in the field of injection moulding plastics is the advent of Servo Motor Technology. This revolutionary innovation eliminates the limitations of conventional hydraulic systems and paves the way for more precise and energy-efficient manufacturing processes. This article delves into the transformative impact of Servo Motor Technology on injection moulding plastics and its potential to revolutionize the industry.I. Background:Injection moulding plastics, a widely adopted manufacturing process, involves the creation of plastic products through the injection of molten material into a mould. Traditionally, hydraulic systems powered by pumps were used to drive the injection process, resulting in limitations such as excess energy consumption, imprecise control, and inconsistent product quality. These shortcomings paved the way for the emergence of an alternative: Servo Motor Technology.II. Servo Motor Technology Explained:Servo motors, unlike hydraulic systems, utilize electrical power to drive the injection process. This cutting-edge technology offers superior control, precision, and efficiency. The servo motor system consists of a motor, an encoder, a controller, and a hydraulic accumulator. The encoder provides real-time data on the position and velocity of the motor, enabling the controller to regulate the injection process accurately. This ensures precise and repeatable positioning of the mould, resulting in uniform product quality.III. Advantages of Servo Motor Technology:1. Energy Efficiency: Servo motors consume considerably less energy compared to traditional hydraulic systems. By closely matching the speed and torque requirements of the injection process, the servo motor system reduces wasteful energy consumption, leading to substantial cost savings for manufacturers.2. Improved Precision and Control: Servo Motor Technology enables precise control over the injection process, offering greater accuracy in terms of shot weight, injection timing, and mould positioning. This not only enhances the overall quality of products but also reduces material waste and rework, making it an environmentally friendly solution.3. Reduced Noise Levels: Servo motors operate more quietly and smoothly as compared to hydraulic systems. This reduction in noise pollution contributes to a safer and more pleasant working environment for operators.IV. Application and Impact:The implementation of Servo Motor Technology drives advancements across various industries that rely on injection moulding plastics. Automotive, consumer goods, electronics, and packaging sectors are among the key beneficiaries of this transformative technology. Automakers benefit from accurate and consistent production of automotive parts, while the consumer goods industry enjoys improved product reliability and efficiency. Electronics manufacturers can achieve precise positioning of complex moulds, leading to enhanced product performance. Furthermore, the packaging industry benefits from increased productivity and minimized material waste.V. Market Outlook:The global injection moulding plastics market is projected to witness substantial growth owing to various factors, including the introduction of innovative technologies like Servo Motor Technology. Manufacturers are showing increased interest in adopting this technology to gain a competitive edge. Furthermore, the rising environmental concerns and stringent regulations related to energy consumption and carbon emissions are expected to propel the demand for energy-efficient solutions such as Servo Motor Technology.Conclusion:As the manufacturing industry seeks to optimize productivity and enhance product quality while minimizing energy consumption, Servo Motor Technology provides an effective solution for injection moulding plastics. The advantages of this groundbreaking technology, including improved precision, energy efficiency, and reduced noise levels, are poised to revolutionize the industry. With its widespread application across various sectors, Servo Motor Technology is set to usher in a new era of efficiency and sustainability in the injection moulding plastics market.
Pc Plastic Injection Mould Display Cover: A Comprehensive Guide
Title: Revolutionary PC Plastic Injection Mould Display Cover Redefines Durability and Efficiency in the Electronics IndustryIntroduction:In the dynamic landscape of the electronics industry, innovation has always been a driving force that shapes and propels businesses forward. Demonstrating a commitment to delivering cutting-edge solutions, [Company Name], a renowned leader in the field of plastic injection molding, has recently launched its groundbreaking PC Plastic Injection Mould Display Cover. This revolutionary product is destined to redefine durability and efficiency, making waves across the industry.The PC Plastic Injection Mould Display Cover is poised to address key challenges faced by the electronics sector, offering incredible mechanical properties, superior heat resistance, and enhanced impact resistance. Designed with impeccable precision, this display cover is created using state-of-the-art plastic injection molding techniques, resulting in a product that is both visually appealing and highly functional.Body:1. Durability and Strength:The PC Plastic Injection Mould Display Cover revolutionizes the electronic device protection landscape by providing unparalleled durability and strength. Manufactured using polycarbonate, a material known for its robust properties, this cover surpasses traditional options currently available on the market. It provides exceptional resistance to scratches, abrasions, and impacts, ensuring the longevity of electronic devices. By shielding delicate displays from accidental drops, harsh environmental conditions, and everyday wear and tear, the cover minimizes the need for costly repairs or replacements, thereby saving both time and resources for end-users.2. Enhanced Heat Resistance:Heat management is a critical aspect in the electronics industry, especially with the increasing processing power and component density of modern devices. The PC Plastic Injection Mould Display Cover possesses outstanding heat-resistant properties, reducing the risk of overheating and ensuring optimal device performance. Equipped with advanced ventilation systems and engineered to dissipate heat effectively, this innovative cover mitigates the potential for heat-related malfunctions. Users can now have peace of mind, knowing that their devices, equipped with this remarkable cover, can endure prolonged usage without compromising efficiency.3. Superior Impact Resistance:One of the common concerns for electronic devices is their vulnerability to accidental damage caused by impacts, drops, or collisions. The PC Plastic Injection Mould Display Cover excels in this area, offering unmatched impact resistance. By employing cutting-edge injection molding techniques, the cover can effectively reduce the impact shock by dispersing it evenly across its surface. This unique feature acts as a protective shield, safeguarding vital internal components and preventing shattered screens in case of accidents. The superior impact resistance provided by this display cover brings reassurance to users, enabling them to confidently use their electronic devices without fear of damage.4. Precision Engineering and Design:The PC Plastic Injection Mould Display Cover showcases the pinnacle of precision engineering and design. [Company Name], renowned for its expertise in plastic injection molding, strategically combines its industry-leading knowledge with the latest technology to create a display cover that seamlessly integrates with various device models. Through meticulous research and development, careful attention is given to ensuring an ergonomic design, guaranteeing an optimal user experience. The precisely engineered fit and finish not only enhance the aesthetics of the device but also prevent dust ingress, providing a clean and seamless display.Conclusion:With the launch of the PC Plastic Injection Mould Display Cover, [Company Name] has set a new standard in the electronics industry. This revolutionary product represents a remarkable leap forward in terms of durability, heat resistance, and impact resistance. Through their commitment to innovation, the company has further solidified its position as a leader in the field of plastic injection molding. As demand for cutting-edge protection solutions continues to rise, the remarkable qualities of this PC Plastic Injection Mould Display Cover are poised to reshape the electronics industry and revolutionize how devices are safeguarded.
Unlocking the Power of Injection Over Molding: A Revolutionary Technique Reshaping the Industry
Title: Innovative Injection Over Molding Revolutionizes Manufacturing ProcessesIntroduction:In today's highly competitive manufacturing industry, companies are constantly seeking innovative solutions to advance their production processes. One such breakthrough is Injection Over Molding, a cutting-edge technique that combines polymers and other materials to enhance product functionality, durability, and aesthetics. Leading the charge in this realm is an industry pioneer, whose commitment to technological advancements has revolutionized the manufacturing landscape.Company Overview:With a rich history spanning several decades, [Company Name] has emerged as a global leader in the manufacturing sector. The company's core ethos revolves around driving innovation and pushing boundaries to deliver state-of-the-art solutions to clients spanning various industries. With a highly skilled team of engineers and technicians, coupled with world-class facilities, [Company Name] has successfully established a track record of excellence, setting new benchmarks in manufacturing.1. Introduction to Injection Over Molding:Injection Over Molding is a groundbreaking technique that combines injection molding with over molding to create complex products with enhanced functionality. It involves injecting molten materials into a mold, effectively encapsulating a pre-formed component or substrate. The result is a seamless integration of multiple materials, providing superior product performance and aesthetic appeal.2. Advantages of Injection Over Molding:a. Enhanced Functionality: The ability to encapsulate multiple materials within a single mold enables the production of products with improved functionality and performance. Injection Over Molding allows for the integration of various materials such as rubber, metal, or electronics into a single component, leading to increased durability and versatility.b. Design Flexibility: With Injection Over Molding, manufacturers can achieve complex designs that would otherwise be difficult or costly to produce. This versatility allows companies to create products that meet specific requirements while maintaining a sleek and ergonomic design.c. Cost Savings: By combining multiple materials into a single mold, manufacturers can reduce production costs associated with assembling multiple components. Additionally, the seamless integration of materials eliminates the need for additional assembly steps, streamlining the production process and decreasing overall manufacturing time.3. Applications of Injection Over Molding:a. Automotive Industry: Injection Over Molding is widely employed in the automotive sector to produce components such as instrument panels, door handles, buttons, and switches. The technique's ability to combine different materials enables manufacturers to create durable and visually appealing parts that enhance the overall driving experience.b. Electronics Industry: The electronics industry extensively utilizes Injection Over Molding for producing casings, connectors, and keypads. The technique ensures enhanced durability against external elements, such as moisture and shock, while maintaining optimal functionality.c. Medical Industry: Injection Over Molding finds applications in the medical field for creating devices such as syringe bodies, ergonomic grips, and electrodes. The seamless integration of materials ensures a safe and hygienic product, while its design flexibility aids in the creation of ergonomic and user-friendly medical equipment.4. The Role of [Company Name] in Advancing Injection Over Molding:As a pioneer in Injection Over Molding, [Company Name] has played a pivotal role in advancing this groundbreaking technique. By harnessing state-of-the-art technology and leveraging their extensive expertise, the company has consistently pushed the boundaries of what is possible in the manufacturing industry.[Company Name]'s commitment to innovation and customer satisfaction has positioned them at the forefront of the industry. Their cutting-edge facilities, research labs, and highly skilled team of engineers enable them to deliver bespoke solutions to clients across various sectors, revolutionizing the way products are manufactured.Conclusion:Injection Over Molding represents an exciting leap forward in manufacturing technology. With its ability to combine multiple materials seamlessly, this technique enhances functionality, design flexibility, and cost-effectiveness, making it highly attractive to industries across the board. Spearheading this revolution, [Company Name] continues to lead the way by delivering groundbreaking solutions that redefine the manufacturing industry's standards.